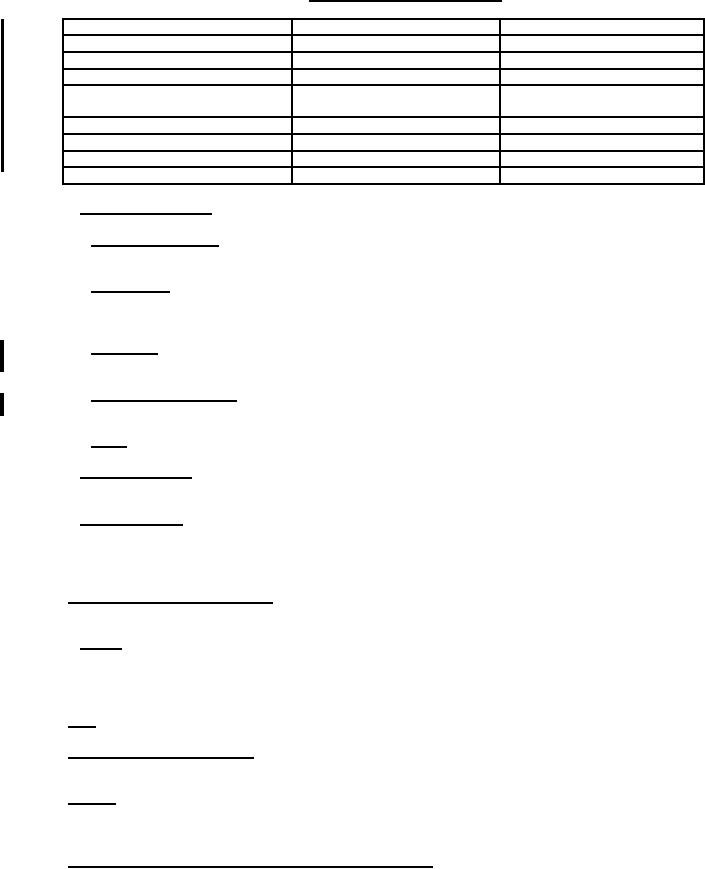
MIL-DTL-24211C
TABLE I. Component materials inspection.
Applicable document
Component material
Requirement paragraph
Aluminum-base alloys:
3.2.1 --
Bar stock and forging
ASTM-B221 or B211
Sand casting
ASTM-B85/B85M, B26/B26M
Die casting
or B108/B108M
Permanent mold casting
3.2.1.4 AST
Sheet
Silicone rubber
Plating
3.2.1 Aluminum-base alloys.
3.2.1.1 Bar stock and forging. When fabricated from bar stock or by forging, gaskets shall be made of an
aluminum alloy conforming to alloy 6061 of ASTM-B221 or ASTM-B211; bar stock shall be temper T6.
3.2.1.2 Sand casting. When fabricated by sand casting, gaskets shall be made of aluminum alloy conforming to
ANSI-H35.1 alloy designation alloys 295.0, condition T4; alloy 208.0, condition F; or alloy 712.0, condition T5 of
3.2.1.3 Die casting. When fabricated by die casting, gaskets shall be made of aluminum alloy conforming to
ASTM-B85/B85M, ASTM-B26/B26M or ASTM-B108/B108M.
3.2.1.4 Permanent mold casting. When fabricated by permanent mold casting, gaskets shall be made of an
aluminum alloy conforming to alloy 356.0, condition T6 or alloy 355.0, condition T6 of ASTM-B108/B108M.
3.2.1.5 Sheet. When fabricated from sheet aluminum, the alloy shall conform to ASTM-B209.
3.2.2 Rubber compound. The rubber compound for the gaskets shall be silicone rubber, class 2A, grade 60, in
accordance with A-A-59588.
3.2.3 Dissimilar metals. Unless suitably protected against electrolytic corrosion, dissimilar metals shall not be
used in intimate contact with each other (see 6.4.1). This pertains to different metals within the gaskets themselves,
as well as to gasket metals in contact with waveguide flange metals. Waveguide flange metal materials are
identified in MIL-DTL-3922.
3.3 Interface and physical dimensions. Gaskets shall be of the design, interface and physical dimensions
3.3.1 Plating. The metal alloy (see 3.7) used shall have equivalent form, fit, functional performance and corrosion
resistance as cadmium plate, type I class 2, in accordance with SAE-AMS-QQ-P-416, of sufficient density to
withstand the salt spray (corrosion) test in 4.6.3 without evidence of corrosion or pitting. Plating must be
accomplished prior to molding the rubber to the metal.
3.4 Seal. When tested as specified in 4.6.4, gaskets shall show no air leakage.
3.5 Radio Frequency (RF) leakage. When tested as specified in 4.6.5, RF leakage shall be at least 100 decibels
(dB) below the transmitted power at the gasket.
3.6 Pure tin. The use of pure tin, as an underplate or final finish, is prohibited both internally and externally. Tin
content of waveguide flange gasket components and solder shall not exceed 97 percent, by mass. Tin shall be
alloyed with a minimum of 3 percent lead, by mass (see 6.6).
3.7 Recycled, recovered, or environmentally preferable materials. Recycled, recovered, or environmentally
preferable materials should be used to the maximum extent possible provided that the material meets or exceeds
the operational and maintenance requirements, and promotes economically advantageous life cycle costs. All
components supplied shall be new and unused.
3
For Parts Inquires submit RFQ to Parts Hangar, Inc.
© Copyright 2015 Integrated Publishing, Inc.
A Service Disabled Veteran Owned Small Business